Unsere Forschungsgebiete
Wir stehen für wissenschaftlich fundierte und praxisnahe Forschung an Polymerwerkstoffen. Wir decken die gesamte Kette von der Materialentwicklung über die Verarbeitung bis zur anwendungsnahen Prüfung ab. Die Nachhaltigkeit ist in allen unseren Forschungsfeldern ein integraler Bestandteil. Verschaffen Sie sich ein Bild von unseren Schwerpunkten.
Polymere Schaumstoffe weisen durch ihre zelluläre Struktur einzigartige Eigenschaften auf. Ihr geringes Gewicht und ihre mechanische Dämpfung gepaart mit ausgezeichneter thermischer und akustischer Isolation macht Schäume für viele Einsatzgebiete attraktiv. Dazu zählen Anwendungen in der Wärmedämmung, der Verpackung, der Schuhtechnologie, im konstruktiven Leichtbau und vielen mehr.
Wir forschen an der gezielten Einstellung von Struktur und Eigenschaften polymere Schaumstoffe. Dafür modifizieren wir Polymere, nutzen existierende Fertigungsprozesse, entwickeln neue Verfahren und untersuchen detailliert die resultierenden Eigenschaften.
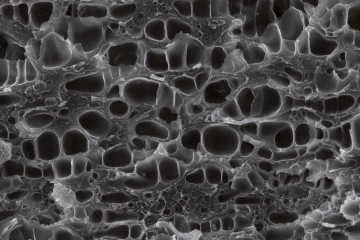
Faserverbundwerkstoffe verbinden geringes Gewicht mit exzellenten mechanischen Eigenschaften und sind deshalb das Material der Wahl für Anwendungen, in denen Leichtbaukonzepte gefragt sind. Das Anwendungsspektrum für faserverstärkte Kunststoffe hat sich in den letzten Jahren rasch vergrößert. Darüber hinaus birgt die Faserverbundbranche auch in der Zukunft noch großes Wachstumspotential.
Wir forschen an Faserverbundwerkstoffen und deren Fertigungstechnologien. Besonderes Augenmerk liegt auf der gezielten Modizierung der Matrix, um beispielsweise die Zähigkeit, die Verarbeitbarkeit oder die Flammschutzeigenschaften des Faserverbundwerkstoffes zu beeinflussen. Unser Wissen über die gezielte Anpassung von Harzsystemen wenden wir mittlerweile auch in anderen Gebieten wie der Medizintechnik an.
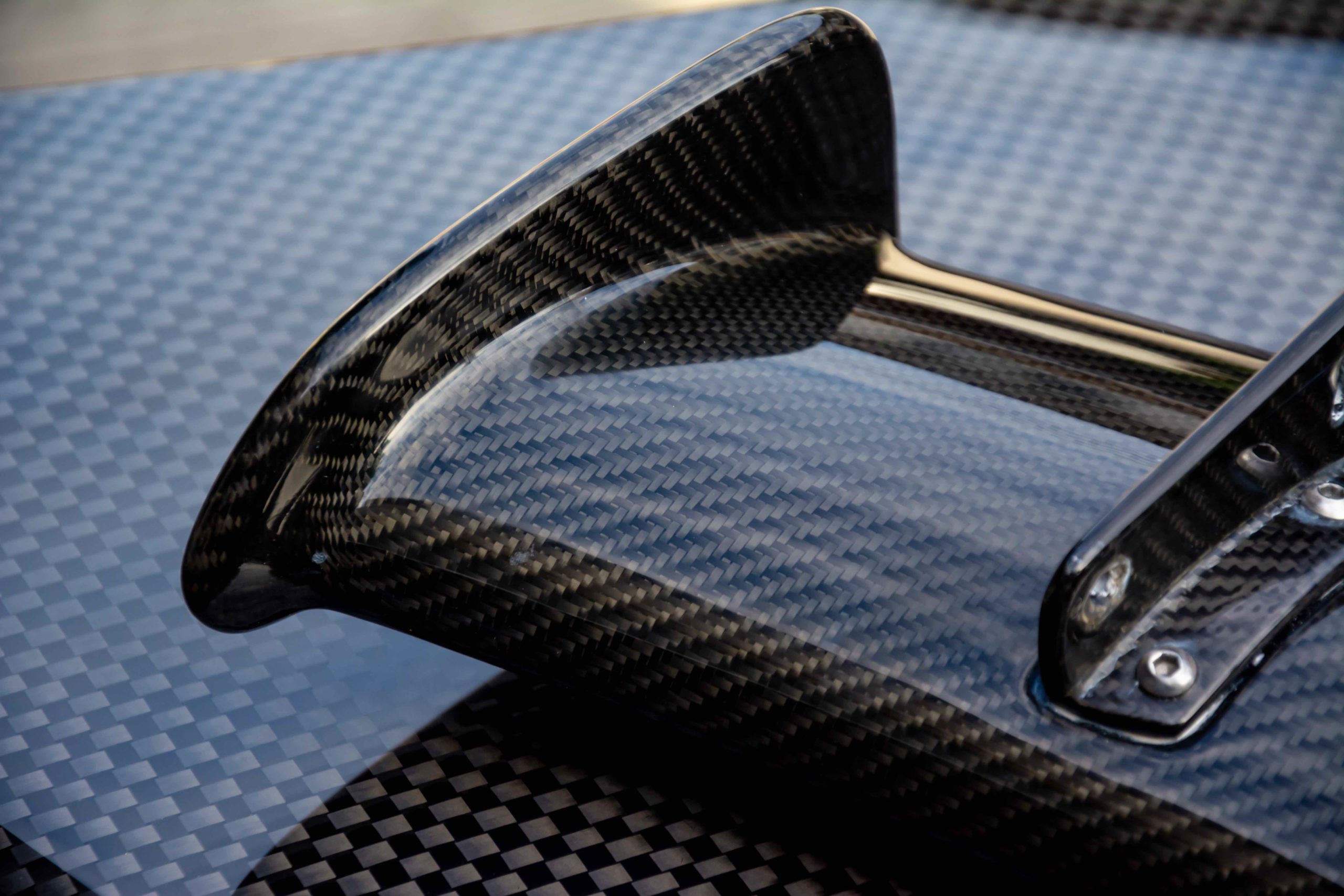
Polymere Werkstoffe können durch Additive und andere Polymere für die Verarbeitung und die Anwendung optimiert werden. Dadurch erfüllen sie anspruchsvollste Anforderungen und ermöglichen neue Einsatzgebiete.
Wir forschen an der gezielten Einstellung der Eigenschaften thermoplastischer Materialien. Diese funktionellen Thermoplaste zeichnen sich durch einzigartige thermische, elektrische, optische, mechanische oder verarbeitungstechnische Eigenschaften aus. Besonders der Einsatz derartiger Materialien in der additiven Fertigung und anderen integrativen Herstellprozessen besitzt bei uns einen hohen Stellenwert.
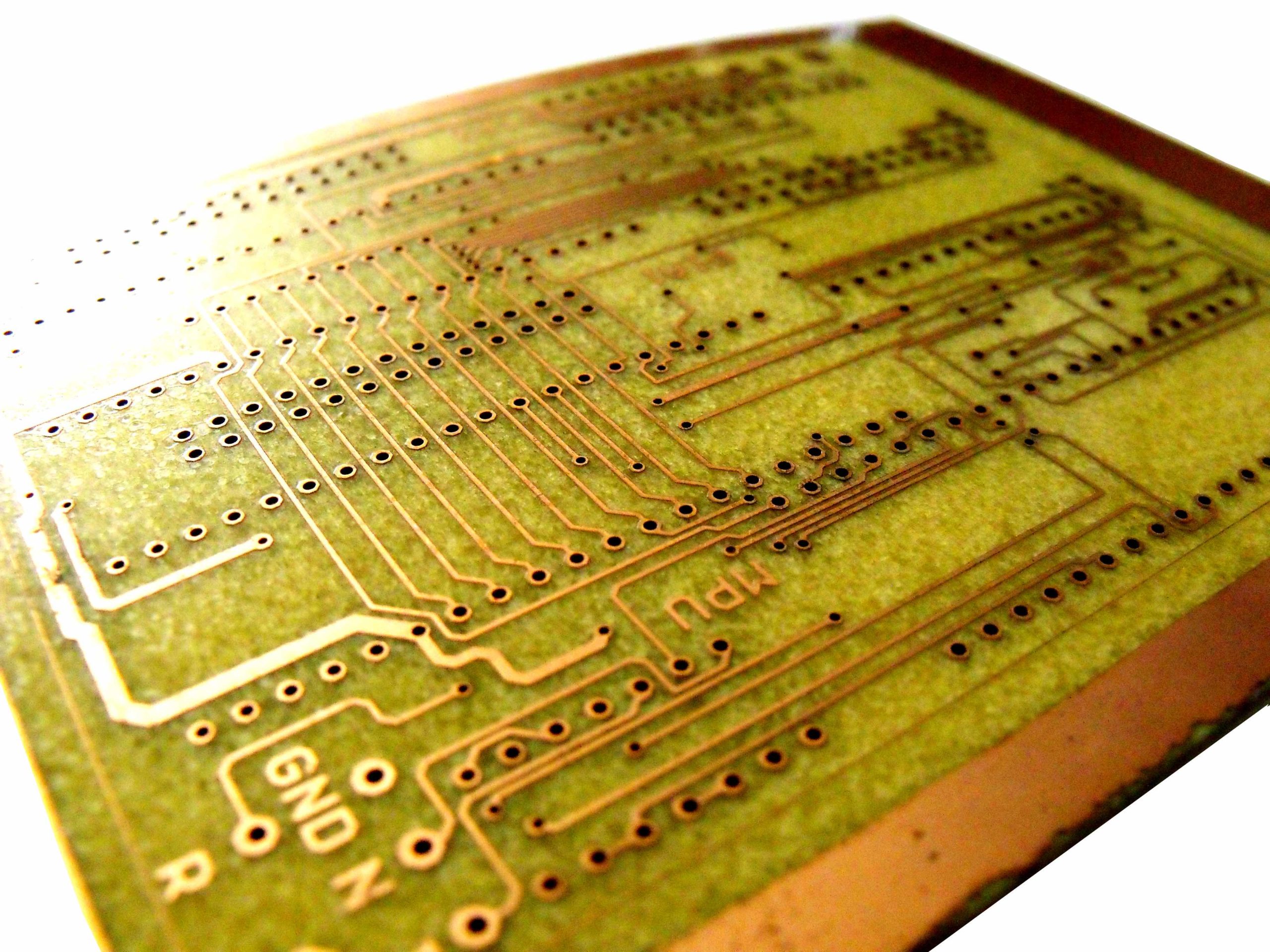
Die Zukunft der Kunststoffindustrie ist vernetzt, das gilt im gleichen Maß für die Polymerforschung. Vernetzt umschließt sowohl Verfahren als auch Daten. Die geschickte Kombination aus unterschiedlichen Technologien, gerade mit neuartigen Verarbeitungsmethoden wie der additiven Fertigung, eröffnet neue Möglichkeiten im Produktdesign. Im gleichen Schritt ist die konsequente Nutzung von Information entlang der gesamten Entwicklungs- und Fertigungskette notwendig.
Wir beschäftigen uns mit den drei Schlüsselthemen – Digitalisierung, integrative und additive Fertigung – um in der Forschung und der Entwicklung von Anwendungen polymerer Werkstoffe neue Akzente zu setzen. Genauso wichtig ist für uns die geschickte Verknüpfung der Themenbereiche.
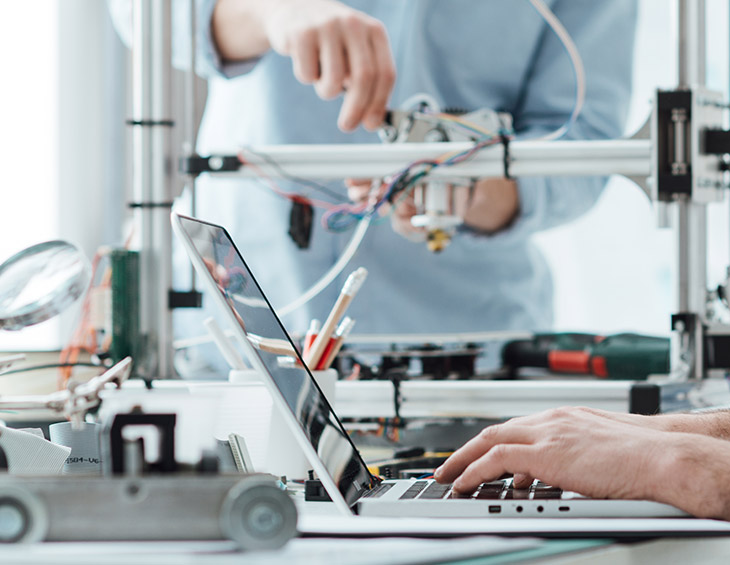
Nachhaltigkeit und Umweltschutz sind im Zusammenhang mit Kunststoffen gerade sehr präsente Schlagworte in der Öffentlichkeit. Die Gesellschaft fordert nachhaltige Konzepte und verbesserte ökologische Fußabdrücke ein. Und ist gleichzeitig daran interessiert, dass das Alleinstellungsmerkmal der Polymere in vielen Anwendung erhalten bleibt.
Wir forschen daher auf drei wichtigen Gebieten, um die Nachhaltigkeit von polymeren Werkstoffen zu analysieren und zu verbessern. Wir untersuchen die Auswirkung existierender Kunststoffprodukte auf die Umwelt, beispielsweise in Form von Mikroplastik. Um die Nachhaltigkeit langfristig zu verbessern, entwickeln wir in unseren unterschiedlichen Forschungsgebieten polymere Lösungen auf Basis biobasierter und bioabbaubarer Ausgangsmaterialien. Und schließlich beschäftigen wir uns mit der Rezyklierung von Polymeren.
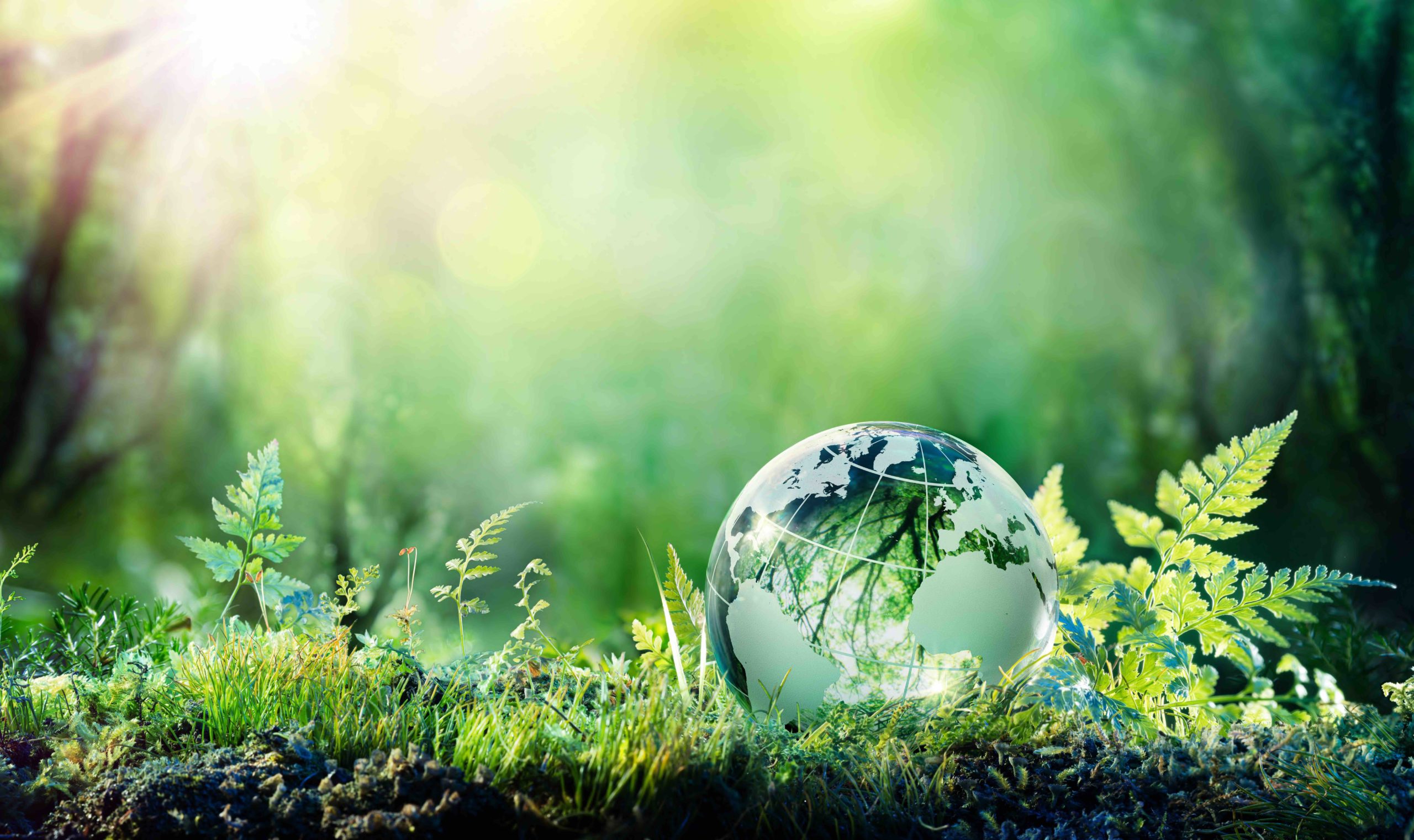